Get reliable results with professional plastic extrusion techniques
Get reliable results with professional plastic extrusion techniques
Blog Article
A Comprehensive Overview to the Process and Benefits of Plastic Extrusion
In the huge world of production, plastic extrusion becomes a very efficient and crucial process. Translating raw plastic into continual profiles, it satisfies a wide variety of sectors with its amazing convenience. This guide aims to clarify the intricate steps associated with this approach, the types of plastic appropriate for extrusion, and the game-changing benefits it gives the sector. The following discussion guarantees to unravel the real-world influences of this transformative procedure.
Understanding the Basics of Plastic Extrusion
While it may appear complicated in the beginning glimpse, the procedure of plastic extrusion is basically straightforward - plastic extrusion. It is a high-volume production strategy in which raw plastic is thawed and formed into a continuous profile. The procedure starts with the feeding of plastic product, in the kind of pellets, granules, or powders, into a heated barrel. The plastic is then thawed making use of a mix of warmth and shear, used by a turning screw. Once the molten plastic gets to completion of the barrel, it is required with a small opening known as a die, shaping it right into a wanted form. The designed plastic is then cooled, strengthened, and reduced into desired sizes, finishing the process.
The Technical Process of Plastic Extrusion Explained
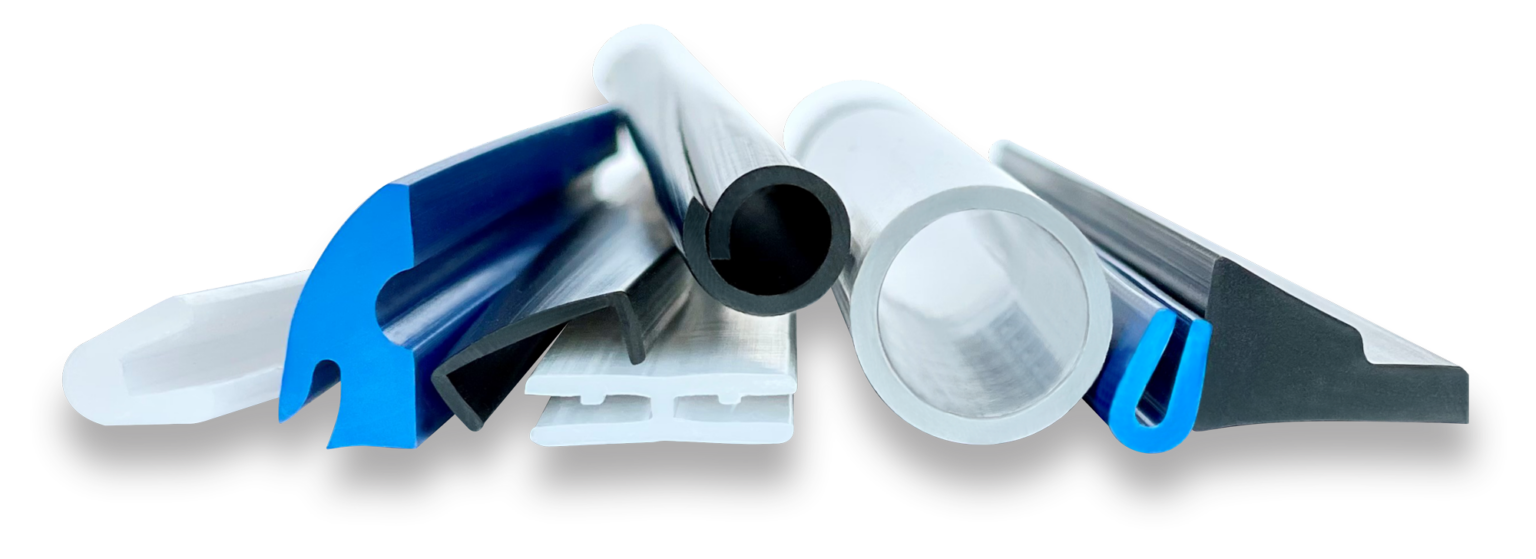
Sorts Of Plastic Suitable for Extrusion
The choice of the best type of plastic is a critical facet of the extrusion process. Numerous plastics provide unique residential or commercial properties, making them more fit to certain applications. Comprehending these plastic types can substantially enhance the extrusion procedure.
Comparing Plastic Extrusion to Other Plastic Forming Methods
Comprehending the kinds of plastic appropriate for extrusion paves the method for a broader conversation on just how plastic extrusion stacks up versus other plastic developing approaches. These include shot molding, impact molding, and thermoforming. Each technique has its one-of-a-kind uses and advantages. Shot molding, for instance, is exceptional for developing elaborate components, while impact molding is ideal for hollow things like bottles. Thermoforming excels at developing shallow or big components. Plastic extrusion is unrivaled when it comes to producing constant accounts, such as pipes, seals, and gaskets. It likewise enables a regular cross-section along the length of the product. Thus, the choice of technique greatly relies on the end-product requirements and specifications.
Trick Advantages of Plastic Extrusion in Production
In the world of production, plastic extrusion uses lots his explanation of considerable benefits. One noteworthy advantage is the cost-effectiveness of the process, which makes it a financially visit this site enticing manufacturing technique. Additionally, this strategy offers premium product flexibility and enhanced production rate, consequently enhancing overall manufacturing efficiency.
Affordable Production Approach
Plastic extrusion jumps to the center as an affordable production technique in production. Furthermore, plastic extrusion calls for much less power than traditional manufacturing techniques, contributing to lower operational prices. Overall, the financial benefits make plastic extrusion a highly attractive option in the manufacturing sector.

Superior Product Flexibility
Beyond the cost-effectiveness of plastic extrusion, another substantial benefit in producing depend on its exceptional product adaptability. This procedure enables the creation of a vast variety of products with differing forms, sizes, and layouts, from easy plastic sheets to detailed profiles. The flexibility is attributed to the extrusion pass away, which can be customized to generate the preferred item style. This makes plastic extrusion a suitable service for sectors that need customized plastic parts, such as automobile, look here construction, and packaging. The capacity to produce varied products is not only useful in conference specific market demands yet likewise in enabling producers to discover new product with minimal funding financial investment. In essence, plastic extrusion's item flexibility promotes innovation while improving functional efficiency.
Boosted Manufacturing Rate
A considerable advantage of plastic extrusion depends on its enhanced production speed. This manufacturing process enables for high-volume manufacturing in a fairly brief time period. It can generating long, continual plastic profiles, which considerably reduces the production time. This high-speed manufacturing is especially beneficial in markets where big quantities of plastic parts are needed within tight due dates. Few other manufacturing processes can match the speed of plastic extrusion. Additionally, the ability to maintain regular high-speed manufacturing without giving up item top quality establishes plastic extrusion in addition to various other approaches. The boosted manufacturing rate, as a result, not only enables producers to meet high-demand orders but additionally adds to boosted effectiveness and cost-effectiveness. This beneficial feature of plastic extrusion has actually made it a favored option in various industries.
Real-world Applications and Impacts of Plastic Extrusion
In the realm of manufacturing, the technique of plastic extrusion holds profound importance. The economic advantage of plastic extrusion, mostly its high-volume and cost-effective output, has transformed manufacturing. The industry is persistently striving for developments in recyclable and naturally degradable materials, suggesting a future where the benefits of plastic extrusion can be kept without jeopardizing environmental sustainability.
Final thought
In final thought, plastic extrusion is a extremely efficient and effective technique of transforming raw materials into varied items. It uses various advantages over other plastic creating techniques, including cost-effectiveness, high output, minimal waste, and design adaptability. Its influence is greatly felt in various industries such as building and construction, auto, and durable goods, making it a pivotal procedure in today's production landscape.
Delving much deeper right into the technical procedure of plastic extrusion, it starts with the option of the proper plastic material. Once cooled, the plastic is reduced into the called for sizes or wound onto reels if the item is a plastic film or sheet - plastic extrusion. Contrasting Plastic Extrusion to Other Plastic Forming Approaches
Recognizing the types of plastic ideal for extrusion paves the way for a more comprehensive discussion on just how plastic extrusion stacks up versus other plastic developing methods. Couple of other production processes can match the rate of plastic extrusion.
Report this page